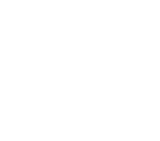
2016
From the period picture below, the original car merely had a hole in the valance for the inlet manifold air intake, which would not prevent stones and other debris from entering the system. The solution was to build and mount a frame with a gauze screen.


A cardboard template was made, which was traced onto a sheet of steel, and then a set of two profiles was cut out. The insides were cut out with a nibbler, then a die grinder and file were used to finish the inside edges. The one frame was then placed inside the valance and formed into shape, which was then copied for the other frame.



Two bolts were welded into the valance to mount the frame, and then two bolts into only one of the frames, which would secure the two frames together. Over time the gauze would have to be replaced, so the frame has been made in such a way that the two frames could come apart. Once completed, the frames were zinc plated.

Stainless-steel gauze used for fly screens was bought from the local hardware store and two pieces were cut out on the bias so that the mesh criss-crossed. These pieces were placed between the frames, bolted together and then fitted to the car.


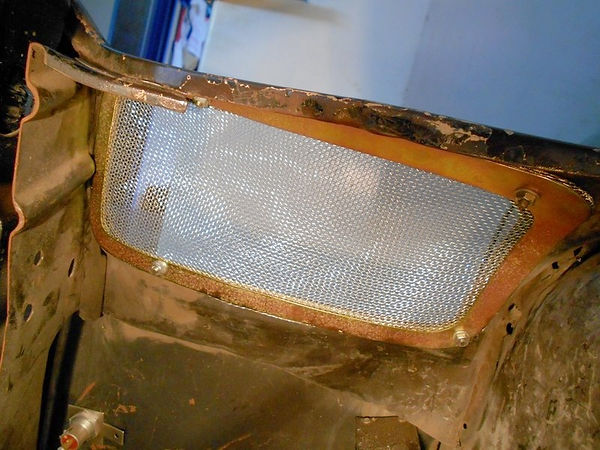
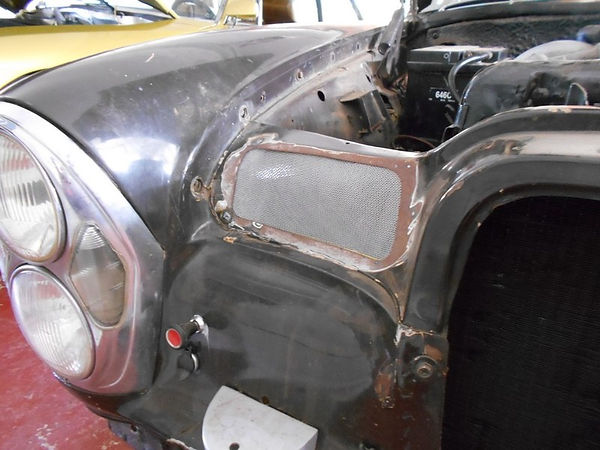
Special adjustable Bilstein shock absorbers were ordered and custom made for the car which have variable damping adjustment. There is a small adjusting knob on the top of the shock which is turned to either give soft or hard damping. It only takes one and a half turns to go from the softest setting to the hardest setting, and the difference is notable when the car is bounced. The bottom mountings are rose-jointed with almost no play and the machined components are a thing of beauty. They fitted perfectly.
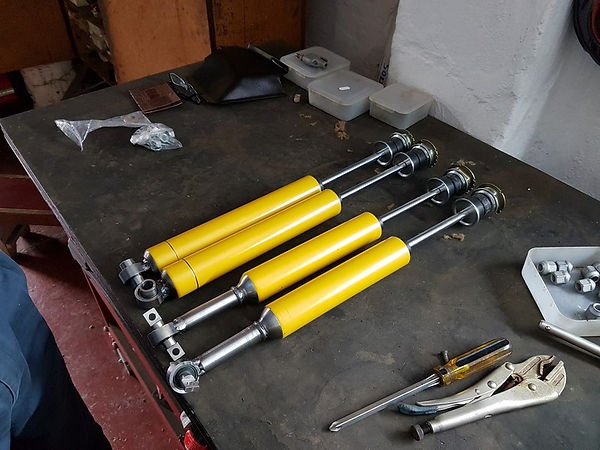


The car was sent for wheel alignment before the first track test. The plan was to put the car on the track and then sort out the basics – see how the car cornered and braked and then do the required changes to the damping to achieve the best results. The same tyre pressures were needed all round and the same damping front and rear. If the car understeered or oversteered, then the damping at the front or the rear needed to be changed in small increments, with the car being driven after each individual change to see what affect the setting change was on the handling.
The first track test arrived amid much excitement and the worst was expected from the car – it was expected to be a handful with air suspension and basic street wheel alignment, as well as unknown damping settings.
What a surprise! After only about two laps of feeling the car out in terms of turning, braking and working out the gear pattern, the car was able to be pushed harder and the car handled very well. It turned out to be very forgiving and turned in well without any understeer.
However, the car was not delivering the sort of horsepower that the chassis could handle. The engine wasn’t revving freely enough over 4500rpm which was probably due to the fuel injection set up. It had been tampered with in the past, so getting it to a specialist to be overhauled and setup properly was required.
The car started to get hot – just above the 100 °C mark, though the radiator had been re-cored with a three-row core. The electric fan worked fine. It was suspected that there was too much under-bonnet heat, for which a solution needed to be found.
The brake pedal needed to be modified to sit closer to the accelerator pedal. The pedals were too wide apart, and it was virtually impossible to heel-and-toe when changing down.
The car weighed in at 1548kg, down from the standard 1765kg. There was still weight saving to be made, like, among other things, replacing the front and rear screens with Lexan.

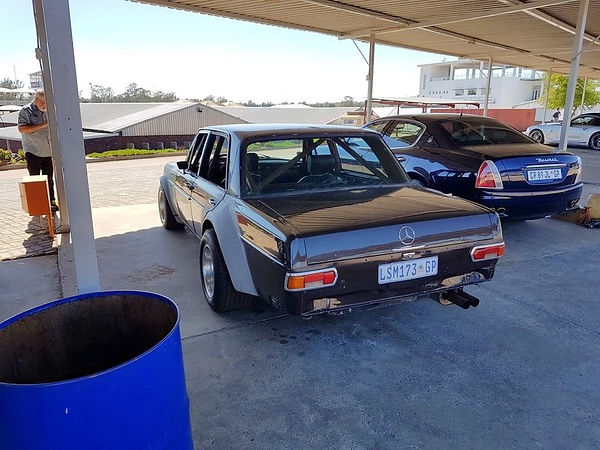
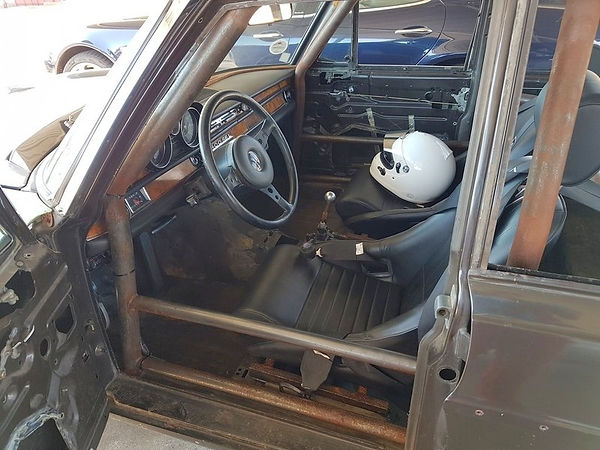
Unmute the video below by tapping on the video and then tapping on the music note in the bottom right corner
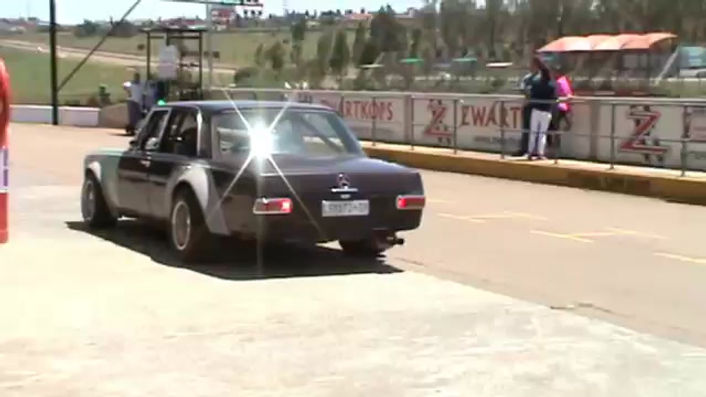
The week after the track test, the car was taken to TW Diesel in Witbank to get the fuel injection sorted out.
The business is owned by Rolf Frommjohann, a German who settled in South Africa many years ago via Namibia. Rolf is an auto electrician by trade but was a research technician for Bosch during the development of the K-Jetronic system. The department was headed up by the engineer who invented the K-Jetronic system and there were five engineers working under him, each with his own research technician.
The fuel injection pumps for the Porsche 917 racers were sent to Bosch after every race to be set up for the next race considering the change in conditions and altitude. This was done in the workshop next to the research centre and Rolf had an arrangement with the technician there that when the Porsche pumps came in, he would be called to see how it was done.
Rolf spent a week with one of the engineers testing and analysing a Kugelfischer fuel injection system, which was strictly forbidden. After he had emigrated to Namibia, he read an article that Kugelfischer had got wind of these tests and Bosch was given a substantial fine by the authorities for having done this.
It was encouraging to see that Rolf’s son was now working with his father, hopefully learning as much as he possible can.

As suspected, the fuel injection system on the 6.3 had been tampered with. The thermostat on the pump was incorrect – it was from a W108 280SE – and the altitude compensator was worn. Inside the pump one of the pistons was misaligned and the steel pipes carrying coolant to the air sensor were totally blocked. The injectors were in very good condition and were probably replaced at some point. The injector mountings were perished and worn – Rolf pointed out that the mountings needed to be 33mm, but most were about 31mm. Some of the ball sockets on the throttle linkages were also worn.
The three-dimensional cam inside the pump was absolutely mind boggling and it can be understood how these cams could be designed and made in today’s world with computers, CAD and multi-plane CNC machines, but these things were worked out with slide rules and made by hand. Astonishing!

The car was collected from TW Diesel a few weeks later and the workmanship was superb. It was surprising to see all the extra detailing work that had been put in.
The coolant pipes that were rusted through had been repaired and plated, along with all the nuts, bolts and screws. The tappet covers and inlet manifolds were chemically cleaned, and the oil filler cap had been polished with all hoses being renewed.
The difference in performance was marked, with the car turning over on a slow idle, but revving to the red like it has never done before. It was still in standard trim but was very quick when driven around the block.

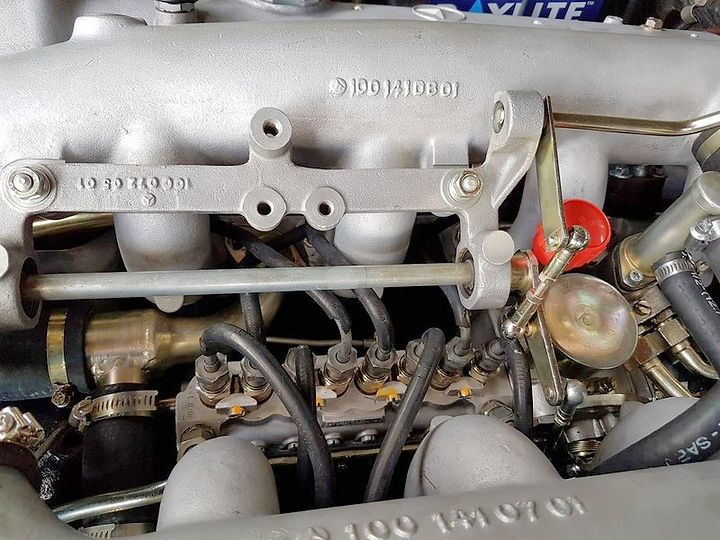
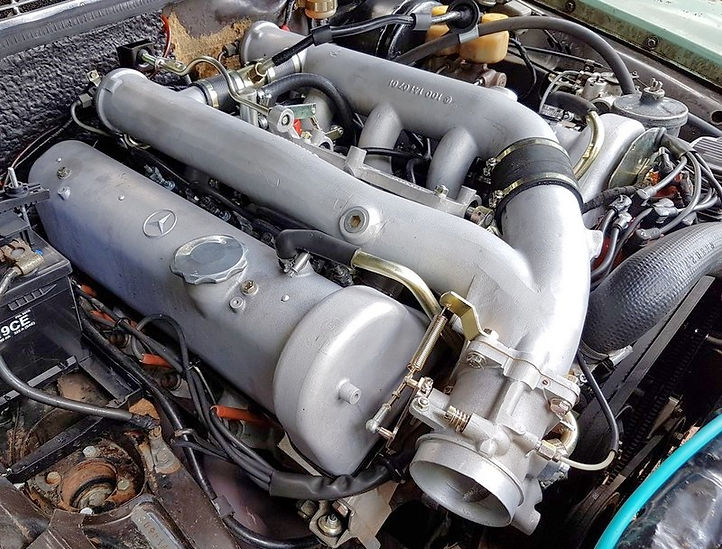
Once the car was back, the modifications discovered during the track test needed to be done.
The brake pedal needed to be closer to the accelerator pedal to be able to heel-and-toe during braking and down shifting. Instead of removing the pedal box assembly, it was decided to bend the brake pedal towards the accelerator pedal in situ. The brake pedal was tensioned with a strap and then heat applied, which bent it into the desired position.
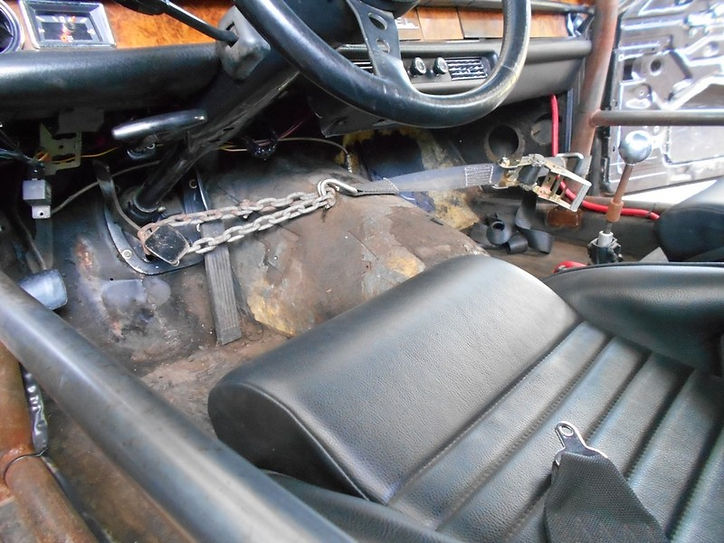


The bonnet and boot lid straps were fitted, and for a bit of inspiration, the spotlights and boot lid badges were also fitted - the car looked pretty much complete.
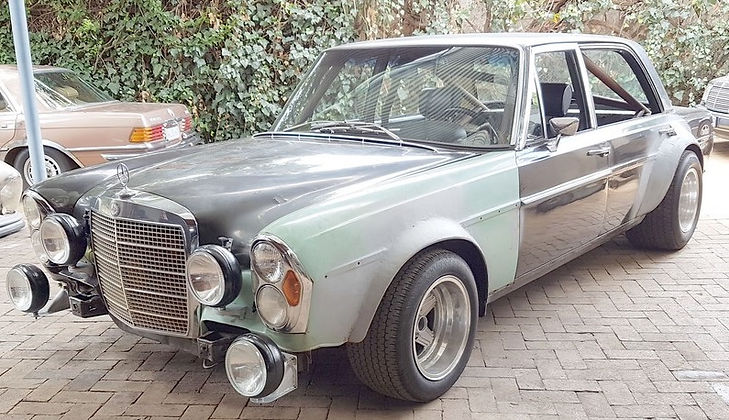
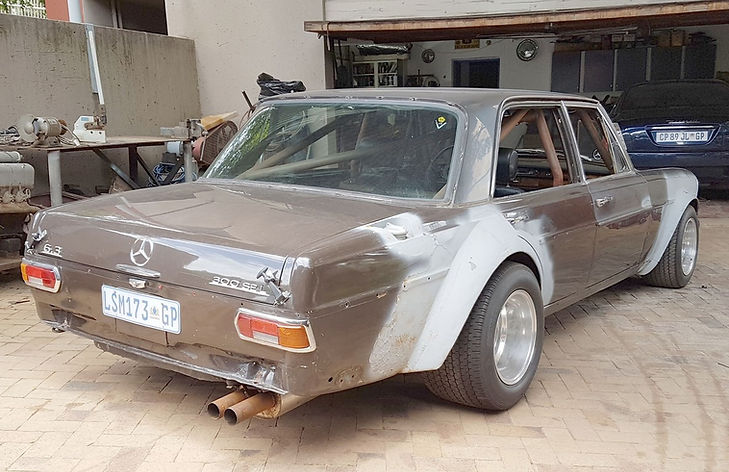
Internet photos show holes drilled into the top left of the front valance, presumably to allow extra airflow to cool the air suspension compressor.
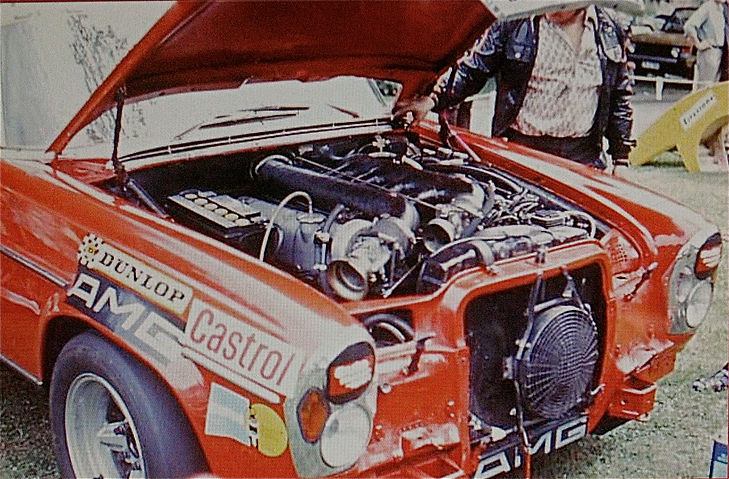
The position of the holes was marked out and drilled, initially with a 6mm drill and then with a 10mm drill.
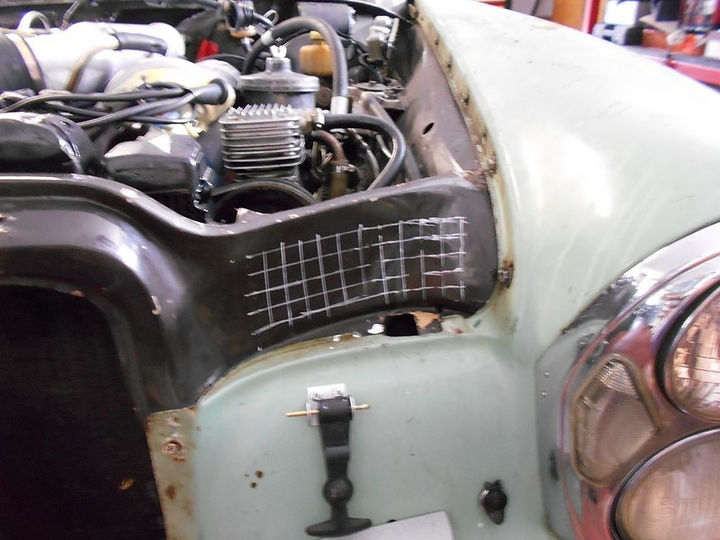
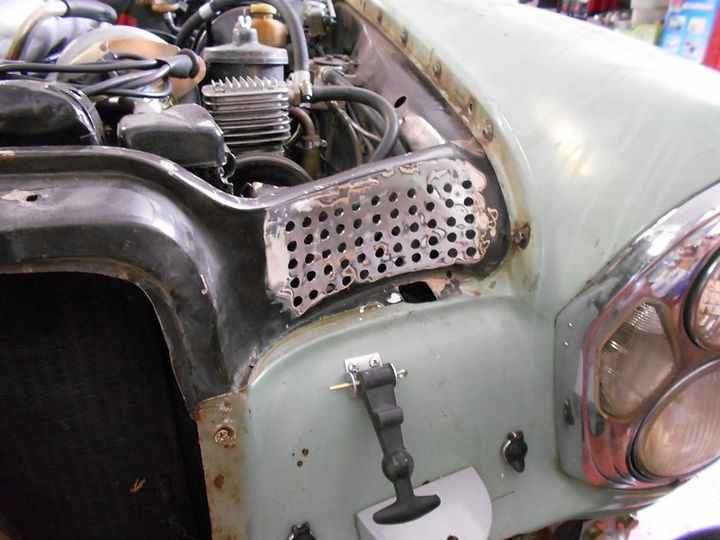
It was decided to relocate the battery to the boot for better weight distribution. At the same time, a centre console that was made during a sheet metalworking course, was also fitted. This still needed to be welded properly and finished off, but fitting it was necessary so that the battery cut-out switch could be installed, a mandatory requirement. Additional switches, like an engine start button, window washer switch and a manual override switch for the engine fan would have to fitted in future. A normal battery cable from the battery to the switch was used, but this was going to be too heavy and would be replaced later.

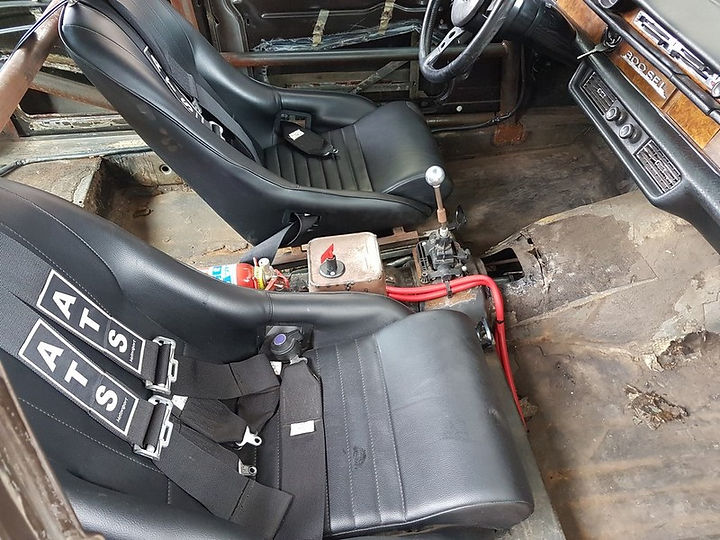
The new battery was the smallest that could practically be used, which was half the size of a normal battery for a 6.3. Adding lightness became a bit of an obsession and losing the original battery tray and mounting brackets had saved almost 1kg.
